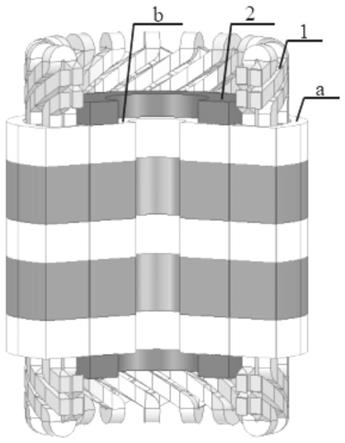
1.本发明涉及电机设备的技术领域,尤其涉及一种新型电动汽车驱动系统非晶合金异步电机。
背景技术:2.全球气候的变化越来越显著,环境破坏和资源短缺引起了人们的普遍关注,全人类的焦点聚集在节约资源和绿色环保这两方面。近年来,国际社会愈来愈重视汽车尾气对大气环境造成的影响,纯电动汽车不需要消耗化石燃料,不会向大气环境排放含有污染物的汽车尾气。
3.目前最多用于电动汽车驱动系统的电机主要有直流电机、永磁同步电机以及异步电机,异步电机结构简单坚固耐用且调速性能与其他电机相比更为出色,因此在电动汽车驱动系统中应用广泛。通过优化电机结构对电机整体效率提升十分有限,可以考虑采用新型材料制作电机来提高电机运行效率。并且硅钢电机工作时,当其频率大于基频,电机的铁芯损耗迅速增大,进而导致铁芯温度的增加,电机所消耗的能源随之提高,限制了电机在高频场合的应用。
4.非晶材料是近期发展起来的一类新型软磁性材料,较硅钢片具备更高的电阻率和磁导率及很小的矫顽力、铁芯损耗,所以采用非晶材料加硅钢片可生产出低损耗、高效率的定子、转子电机铁芯,节约资源。并且旧电机的硅钢片可以重复利用可有效降低电机成本,减少资源浪费。
5.非晶合金具有优越的软磁性能,其磁导率、电阻较硅钢高,矫顽力、铁损较硅钢片小,其中铁损仅为硅钢片的25%左右。但由于非晶合金的饱和磁密低于普通硅钢的饱和磁密,若直接将硅钢铁芯换为非晶合金材料,虽电机损耗减小了,但是会引起电机的转矩下降。这不符合电动汽车高密度电机要求。
6.实际上,由于上述情况,目前针对高密度异步电机主要还处在研发阶段。
技术实现要素:7.针对上述技术问题,本发明的目的在于提供一种结构简单的新型电动汽车驱动系统非晶合金异步电机,能够在充分利用原有异步电机拆卸下的硅钢片的同时,使异步电机的性能及效率得到有效提升。
8.为实现上述目的,本发明提供了一种新型电动汽车驱动系统非晶合金异步电机,包括定子铁芯和转子铁芯,所述定子铁芯结构包括由多片硅钢片相互叠压形成的硅钢叠片铁芯段a1、由多片铁基非晶合金片相互叠压形成的铁基非晶合金铁芯段a2;所述转子铁芯包括由多片硅钢片相互叠压形成的硅钢叠片铁芯段b1、由多片铁基非晶合金片相互叠压形成的铁基非晶合金铁芯段b2;所述硅钢叠片铁芯段a1设置在所述定子铁芯的两端,所述硅钢叠片铁芯段b1设置在所述转子铁芯的两端;在定子铁芯中,所述铁基非晶合金铁芯段a2占定子铁芯的体积分数为30%
‑
50%;在转子铁芯中,所述铁基非晶合金铁芯段b2占转子铁
芯的体积分数为30%
‑
50%。
9.优选的,所述硅钢叠片铁芯段和铁基非晶合金铁芯段均为圆环形段,各圆环形段的轴向长度相等。
10.优选的,所述硅钢叠片铁芯段中每片硅钢片的厚度为0.2mm,所述铁基非晶合金铁芯段中每片铁基非晶合金片的厚度为0.03mm。
11.进一步的,利用废旧的异步电机中的普通硅钢片经展平、酸洗或物理处理去除表面涂层;在950℃的温度下进行去应力退火,保温时间为4小时,保护气体为氮气;随炉冷却至室温,再经切割成型并重新涂覆新涂层完成处理,形成再制造得到所述硅钢片。
12.优选的,所述铁基非晶合金铁芯段的制作包括以下步骤:
13.步骤1:确定用于神经网络模型的铁基非晶合金的基础数据;
14.步骤2:根据获得的基础数据,通过神经网络模型,确定数据间的相关性预测材料宏观性能,建立数据库;
15.步骤3:根据数据库,选择铁基非晶合金成分,筛选出饱和磁感应强度接近硅钢材料,矫顽力低于硅钢材料的铁基非晶合金成分配比;铁基非晶合金的基础数据包括铁基非晶合金原组成元素配比,饱和磁感应强度,矫顽力;
16.步骤4:根据神经网络模型反推出最终的铁基非晶合金分子化学式,多片铁基非晶合金片相互叠压形成铁基非晶合金块,铁基非晶合金块线切割加工成铁基非晶合金铁芯段。
17.与已有技术相比,本发明的有益效果体现在:
18.1.由于非晶合金较低的铁芯损耗和饱和磁密,对于定转子铁芯的磁通密度设计值低于非晶合金饱和磁密的再制造电机,本发明将经拆卸的废旧电机的硅钢定转子铁芯替换为叠压定转子铁芯,额定转速时定转子铁芯损耗是原来的40%
‑
60%,随着转速的增加节能效果更明显,使得再制造后电机效率提高2%左右,对于定转子铁芯的磁通密度设计值高于非晶合金饱和磁密的再制造电机,叠压定子铁芯减少了直接采用非晶合金替换造成的转矩收缩,并提高了电机效率。
19.2.本发明中叠压定转子铁芯在轴向最外端设置为旧硅钢叠片段,并均匀间隔排列,有效避免了因非晶合金叠片薄、脆等可能带来的问题,能有效保护非晶合金段铁芯,并能有效提高非晶合金的叠压系数。
20.3.本发明不仅显著改善了原有电机的能效和性能,而且还充分利用了旧电机的零部件。
21.4.本发明利用神经网络模型来设计铁基非晶合金,降低了铁基非晶合金材料的研发成本,同时避免了依靠经验估算非晶合金性能存在较大误差。
附图说明
22.图1为本发明的新型电动汽车驱动系统非晶合金异步电机的结构示意图;图中a为定子铁芯、b为转子铁芯、1为定子绕组、2为转子绕组;
23.图2为本发明的新型电动汽车驱动系统非晶合金异步电机的定子铁芯结构剖面图;图中a1为硅钢叠片铁芯段、a2为铁基非晶合金铁芯段、3为非晶合金异步电机定子槽;
24.图3为本发明的新型电动汽车驱动系统非晶合金异步电机的转子铁芯结构剖面
图;图中b1为硅钢叠片铁芯段、b2为铁基非晶合金铁芯段、4为非晶合金异步电机转子槽;
25.图4为本发明利用神经网络设计铁基非晶合金的流程示意图;
26.图5为本发明的新型电动汽车驱动系统非晶合金异步电机的外特性曲线图,其中(a)为转速
‑
转矩特性曲线,(b)为转速
‑
功率特性曲线;
27.图6为原异步电机与本发明的新型电动汽车驱动系统非晶合金异步电机的总损耗曲线对比图,其中(a)为原异步电机,(b)为本发明的异步电机。
具体实施方式
28.本发明提供一种新型电动汽车驱动系统非晶合金异步电机,用于连续采煤机的截割试验,下面参见图1~图6对本发明所述新型电动汽车驱动系统非晶合金异步电机进行详细说明。
29.如图1
‑
6所示,本发明的新型电动汽车驱动系统非晶合金异步电机包括定子铁芯a和转子铁芯b,定子铁芯a是由经拆卸的废旧电机的硅钢叠片铁芯与非晶合金铁芯在轴向相互间隔叠压而成。转子铁芯b是由拆卸的废旧电机的硅钢叠片铁芯与非晶合金铁芯在轴向相互间隔叠压而成。
30.如图2所示,定子铁芯a包括由多片硅钢片相互叠压形成的硅钢叠片铁芯段a1、由多片铁基非晶合金片相互叠压形成的铁基非晶合金铁芯段a2,以硅钢叠片铁芯段a1和铁基非晶合金铁芯段a2共同叠压形成定子铁芯(铁芯硅钢片即是指经拆卸的废旧电机的硅钢铁芯中的硅钢片)。
31.如图3所示,转子铁芯b包括由多片硅钢片相互叠压形成的硅钢叠片铁芯段b1、由多片铁基非晶合金片相互叠压形成的铁基非晶合金铁芯段b2,以硅钢叠片铁芯段b1和铁基非晶合金铁芯段b2,共同叠压形成转子铁芯。
32.定子铁芯a在两端分别设置为硅钢叠片铁芯段a1,由于铁基非晶合金叠片材料薄、硬、脆导致铁基非晶铁芯叠压系数较低、容易断裂剥落,将定子铁芯a两端设置为硅钢叠片铁芯段a1,能起到保护非晶合金材料并提高铁基非晶合金铁芯段a2的叠压系数的作用。
33.在定子铁芯a中,铁基非晶合金铁芯段a2占定子铁芯a的体积分数为30%
‑
50%,再制造主要目的之一是在于节约材料,为了使得旧硅钢片大量循环再利用,硅钢叠片铁芯段a1的体积分数下限为50%,尽管铁基非晶合金材料损耗仅是硅钢材料损耗的25%左右,但是其饱和磁密偏低会造成电机转矩降低,为了减少再制造电机转矩降低并提高电机效率,铁基非晶合金铁芯段a2的体积分数上限为50%。
34.硅钢叠片铁芯段和铁基非晶合金铁芯段均为圆环形段,各圆环形段的轴向长度相等。由于两种软磁材料的磁化特性不同,导致不同材料铁芯段及气隙磁场分布不同,为了保证铁芯电机轴向磁场的对称性,消除不同材料造成的电机内轴向磁场的不对称性,设置每段定子铁芯的轴向长度相等。
35.设置定子铁芯a中的硅钢叠片铁芯段a1中每片硅钢片的厚度为0.2mm,铁基非晶合金铁芯段a2中每片铁基非晶合金片的厚度为0.03mm。
36.转子铁芯b在两端分别设置为硅钢叠片铁芯段b1,由于铁基非晶合金叠片材料薄、硬、脆导致铁基非晶铁芯叠压系数较低、容易断裂剥落,将转子铁芯b两端设置为硅钢叠片铁芯段b1,能起到保护非晶合金材料并提高铁基非晶合金铁芯段b2的叠压系数的作用。
37.在转子铁芯b中,铁基非晶合金铁芯段b2占转子铁芯b的体积分数为30%
‑
50%,再制造主要目的之一是在于节约材料,为了使得旧硅钢片大量循环再利用,硅钢叠片铁芯段b1的体积分数下限为50%,尽管铁基非晶合金材料损耗仅是硅钢材料损耗的25%左右,但是其饱和磁密偏低会造成电机转矩降低,为了减少再制造电机转矩降低并提高电机效率,铁基非晶合金铁芯段b2的体积分数上限为50%。
38.硅钢叠片铁芯段和铁基非晶合金铁芯段均为圆环形段,各圆环形段的轴向长度为相等。由于两种软磁材料的磁化特性不同,导致不同材料铁芯段及气隙磁场分布不同,为了保证铁芯电机轴向磁场的对称性,消除不同材料造成的电机内轴向磁场的不对称性,设置每段转子铁芯的轴向长度相等。
39.设置转子铁芯b中的硅钢叠片铁芯段b1中每片硅钢片的厚度为0.2mm,铁基非晶合金铁芯段b2中每片铁基非晶合金片的厚度为0.03mm。
40.定子铁芯a、转子铁芯b均沿轴向分段设置,硅钢叠片铁芯段a1与硅钢叠片铁芯段b1的长度相等并且处在相同的轴向位置;铁基非晶合金铁芯段a2与铁基非晶合金铁芯段b2的长度相同并且处在相同的轴向位置。
41.本发明一方面充分利用了旧电机硅钢片,另一方面由于铁基非晶合金优异的低损耗特性,使得叠压定、转子铁芯损耗是原定、转子铁芯损耗的40%
‑
60%,使得再制造后电机效率提高2%左右。
42.本发明的硅钢片是由废旧的异步电机中的普通硅钢片经展平、酸洗或物理处理去除表面涂层;在950℃的温度下进行去应力退火,保温时间为4小时,保护气体为氮气;随炉冷却至室温,再经切割成型并重新涂覆新涂层完成处理。
43.如图4所示,本发明的铁基非晶合金铁芯段是利用神经网络模型选择以fe、si、b、p四种元素设计一种饱和磁感应强度接近硅钢材料,矫顽力低于硅钢材料的铁基非晶合金,其制作包括以下步骤:
44.步骤1:确定用于神经网络模型的铁基非晶合金的基础数据;
45.步骤2:根据获得的基础数据,通过神经网络模型,确定数据间的相关性预测材料宏观性能,建立数据库;
46.步骤3:根据数据库,选择铁基非晶合金成分,筛选出饱和磁感应强度接近硅钢材料,矫顽力低于硅钢材料的铁基非晶合金成分配比;铁基非晶合金的基础数据包括铁基非晶合金原组成元素配比,饱和磁感应强度,矫顽力;
47.步骤4:根据神经网络模型反推出最终的铁基非晶合金分子化学式,多片铁基非晶合金片相互叠压形成铁基非晶合金块,铁基非晶合金块线切割加工成铁基非晶合金铁芯段。
48.叠压定、转子铁芯的段数取决于再制造电机定、转子铁芯的磁通密度设计值,以电机效率提升且转矩满足要求为目标取得最优段数。此外,铁基非晶合金铁芯也可以换成其他性能优越的软磁材料。
49.以上所述仅为本发明的较佳实施例,并不用以限制本发明,凡在本发明的精神和原则之内,所作的任何修改、等同替换、改进等,均应包含在本发明的保护范围之内。