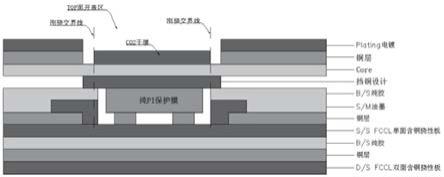
1.本发明涉及线路板制作技术领域,具体为一种内嵌焊盘式刚挠结合板的工艺方法。
背景技术:2.对于内嵌式焊盘的刚挠结合板在流程设计及生产过程中,存在刚性板区的单面式开盖设计、次内层焊盘的表面处理、core板的挡铜设计等诸多问题。 刚性板焊盘区揭盖过程易出现手工揭盖困难、焊盘划伤、金面残胶等产品品质以及外观异常等问题,直接影响生产效率和产品良率。目前行业内暂无该类产品妥善的设计方案和生产模式。
技术实现要素:3.本发明提供一种产品品质好且生产效率高的内嵌焊盘式刚挠结合板的工艺方法。
4.为了实现上述目的,通过以下技术方案实现。
5.一种内嵌焊盘式刚挠结合板的工艺方法,先分别进行挠性基板、纯胶、纯pi保护膜、core板的制作,然后将在制得的挠性基板的两面分别依次叠放纯pi保护膜、纯胶和core板进行压合处理,制得压合后的刚挠结合板,然后对刚挠结合板进行外层制作完成刚挠结合板的完整制作,其中,在所述挠性基板的制作时,线路工序在挠性板区同步蚀刻出内嵌式焊盘,然后进行aoi检查,并在aoi检查后对带有内嵌式焊盘的挠性基板外层铜层进行阻焊印刷,使位于刚挠交界线位置上的铜皮印有阻焊油墨,挠性基板制作完成后,在内嵌式焊盘区域贴合纯pi保护膜;在core板的制作时,cores板一面设计为全铜,另一面只在挠性板区进行挡铜设计,且挡铜区域延伸进刚性板,而在core板线路制作时,在挠性板区只做设计有挡铜的一面,另一面采用干膜曝光保护;在刚挠结合板的外层制作时,采用co2镭射控深开盖方式进行挠性板区的揭盖,co2镭射时,不击穿挡铜层,所述挡铜层在后工序酸性蚀刻时蚀刻去除,其中top面和bot面的揭盖分别单独制作。
6.进一步地,所述挠性基板的制作包括挠性板和挠性板外层的制作,其中,所述挠性板的制作为在双面含铜fccl板的两面均依次叠放纯胶和单面含铜fccl板,然后进行第一次压合处理,得到未制作外层的挠性板,其中,所述单面含铜fccl板无铜层的一面贴合在纯胶层上,所述单面含铜fccl板含铜层的一面远离纯胶层;所述挠性板外层的制作为在挠性基板外层线路制作时在所述挠性基板外层铜层上采用蚀刻工序在挠性区蚀刻出内嵌式焊盘,然后进行aoi检查,并在aoi检查后对带有内嵌式焊盘的挠性基板外层铜层进行阻焊印刷,使位于刚挠交界线位置上的铜皮印有阻焊油墨。
7.进一步地,所述挠性板外层流程在线路制作前还包括打靶—裁边—第一次棕化—
co2镭射—沉铜—填孔电镀,在阻焊印刷工序后还包括后固化—贴抗镀干膜—沉金—退膜—打t孔—第二次棕化—贴纯胶—快压—撕pet膜。
8.进一步地,所述纯胶的制作:流程为裁切—将备在pet膜上的纯胶打t孔—cnc切型—备pet膜,其中,cnc切型工序将对应刚性板次内层焊盘及挠性板开盖区域进行捞空,形成有捞空区域的纯胶,备pet膜工序为在纯胶捞空后,纯胶无pet膜的一面贴合在备pet膜上,然后揭掉捞空后残缺的pet膜,使纯胶一面有pet膜,另一面无pet膜,在后续贴纯胶工序,将纯胶无pet膜的一面贴合在挠性基板上。
9.进一步地,所述纯pi保护膜的制作:流程为裁切—将备在pet膜上的纯pi打t孔—esi镭射控深切型—备pet膜,其中,裁切工序为将纯pi保护膜裁切成片状,且纯pi保护膜片状尺寸小于刚挠结合板的挠性板区尺寸,用于贴合在挠性板区的内嵌式焊盘上;esi镭射控深切型工序为将pet膜对应刚性板次内层焊盘除外的区域的纯pi保护膜全镭,对pet膜进行半镭,保证pet膜不镭断,然后将全镭后的纯pi保护膜无pet膜的一面贴合在备pet膜上,再将纯pi保护膜上另一面半镭后的残缺pet膜揭掉,使纯pi保护膜一面有pet膜,另一面无pet膜,贴合时,将出pi保护膜无pet膜的一面贴在内嵌式焊盘上。
10.进一步地,所述core板的制作:流程为开料—钻孔—曝光/显影,将挡铜位置显影出来—选镀—线路—打t孔—棕化,制得一面为全铜面,一面为只有挡铜区域含铜其它区域为底板的core板。
11.进一步地,所述挡铜设计的挡铜延伸进刚性板0.15mm,所述core板为单面线路设计,所述挡铜设计的一面仅在挡铜区域进行线路设计,所述core板设计挡铜的一面与纯胶和纯pi保护膜贴合。
12.进一步地,所述刚挠结合板的外层制作流程为打靶—裁边—棕化—co2镭射—压膜/曝光/显影—沉铜—填孔电镀—线路—aoi—阻焊印刷—后固化—co2镭射控深开盖—等离子除胶—喷砂前处理—压膜/曝光/显影—酸性蚀刻—aoi—cnc切开盖槽—喷砂前处理—镍钯金—压膜/曝光—cnc成型—退膜—切型—成品水洗—整平烘烤—包装。
13.进一步地,所述co2镭射控深开盖在挠性板区的开盖区设计co2镭射路径,co2镭射路径外缘与两侧的刚挠交界线重合。
14.进一步地,所述co2镭射的光斑大小为0.15mm,相邻光斑相交,相交重合区域为光斑大小的3/4。
15.本发明内嵌焊盘式刚挠结合板的工艺方法与现有技术相比,具有如下有益效果:本发明内嵌焊盘式刚挠结合板的工艺方法通过在挠性基板外层线路制作时,在挠性基板位于挠性板区的外层铜层位置同步蚀刻出焊盘,并在挠性基板位于挠性板区外的刚挠交界线位置外的铜皮上印阻焊油墨,使焊盘在挠性基板与纯胶、core板压合后形成内嵌式焊盘,有效解决了现有技术中焊盘位于板最外层易出现的焊盘划伤问题;core板制作时,一面设计为全铜面,另一面只在挠性区进行挡铜设计,挠性区挡铜的设计,有效避免后续co2镭射控深开盖时击穿挠性基板,确保产品品质,为后续揭盖提供保障;在co2镭射时,不击穿挡铜层,挡铜层在后工序酸性蚀刻时蚀刻去除,然后进行揭盖,该种co2镭射加酸性蚀刻去除挡铜层的技术方案,整个过程无需手工揭盖,无需返工,制程能力高,效率高,而且有效确保产品品质,提高产品良率。
附图说明
16.附图1为本发明内嵌焊盘式刚挠结合板的工艺方法中覆盖膜整面贴合的叠构示意图。
具体实施方式
17.下面将结合具体实施例及附图对本发明内嵌焊盘式刚挠结合板的工艺方法作进一步详细描述。
18.参照图1,本发明一非限制实施例,一种内嵌焊盘式刚挠结合板的工艺方法,先分别进行挠性基板、纯胶、纯pi保护膜、core板的制作,然后将在制得的挠性基板的两面分别依次叠放纯pi保护膜、纯胶和core板进行压合处理,制得压合后的刚挠结合板,然后对刚挠结合板进行外层制作完成刚挠结合板的完整制作,其中,在所述挠性基板的制作时,线路工序在挠性板区同步蚀刻出内嵌式焊盘,然后进行aoi检查,并在aoi检查后对带有内嵌式焊盘的挠性基板外层铜层进行阻焊印刷,使位于刚挠交界线位置上的铜皮印有阻焊油墨,挠性基板制作完成后,在内嵌式焊盘区域贴合纯pi保护膜;在core板的制作时,core板一面设计为全铜,另一面只在挠性板区进行挡铜设计,且挡铜区域延伸进刚性板,而在core板线路制作时,在挠性板区只做设计有挡铜的一面,另一面采用干膜曝光保护,其中,core板设计为全铜的一面为外层,进行挡铜设计的一面为内层,与纯pi保护膜和纯胶贴合;在刚挠结合板的外层制作时,采用co2镭射控深开盖方式进行挠性板区的揭盖,co2镭射时,不击穿挡铜层,所述挡铜层在后工序酸性蚀刻时蚀刻去除,其中top面和bot面的揭盖分别单独制作,由于刚挠结合板两面焊盘设置不同,因此top面和bot面的揭盖分别根据各面的焊盘设置进行相应制作。
19.本发明内嵌焊盘式刚挠结合板的工艺方法通过在挠性基板外层线路制作时,在挠性基板位于挠性板区的外层铜层位置同步蚀刻出焊盘,并在挠性基板位于挠性板区外的刚挠交界线位置外的铜皮上印阻焊油墨,使焊盘在挠性基板与纯胶、core板压合后形成内嵌式焊盘,有效解决了现有技术中焊盘位于板最外层易出现的焊盘划伤问题;core板制作时,一面设计为全铜面,另一面只在挠性区进行挡铜设计,挠性区挡铜的设计,有效避免后续co2镭射控深开盖时击穿挠性基板,确保产品品质,为后续揭盖提供保障;在co2镭射时,不击穿挡铜层,挡铜层在后工序酸性蚀刻时蚀刻去除,然后进行揭盖,该种co2镭射加酸性蚀刻去除挡铜层的技术方案,整个过程无需手工揭盖,无需返工,制程能力高,效率高,而且酸性蚀刻工序有效蚀刻干净前工序co2控深镭射产生的残铜,有效确保产品品质,提高产品良率。
20.参照图1,本发明一非限制实施例,所述挠性基板的制作包括挠性板和挠性板外层的制作,其中,所述挠性板的制作为在双面含铜fccl板的两面均依次叠放纯胶和单面含铜fccl板,然后进行第一次压合处理,得到未制作外层的挠性板,其中,所述单面含铜fccl板无铜层的一面贴合在纯胶层上,所述单面含铜fccl板含铜层的一面远离纯胶层;所述挠性板外层的制作为在挠性基板外层线路制作时在所述挠性基板外层铜层
上采用蚀刻工序在挠性区蚀刻出内嵌式焊盘,然后进行aoi检查,并在aoi检查后对带有内嵌式焊盘的挠性基板外层铜层进行阻焊印刷,使位于刚挠交界线位置上的铜皮印有阻焊油墨。
21.参照图1,本发明一非限制实施例,所述挠性板外层流程在线路制作前还包括打靶—裁边—第一次棕化—co2镭射—沉铜—填孔电镀,其中,第一次棕化保证单面含铜板fccl板上的底铜,使co2镭射可直接破铜;在阻焊印刷工序后还包括后固化—贴抗镀干膜—沉金—退膜—打t孔—第二次棕化—贴纯胶—快压—撕pet膜,其中贴抗镀干膜选用co2干膜,制作时,在单面含铜fccl板上挠性板区贴上抗镀干膜,为后续co2镭射开盖提供保障,提高效率,而打t孔工序的目的是为了挂pin对位,第二次棕化是用于粗化板面,为后续贴纯胶增加粘结力。
22.参照图1,本发明一非限制实施例,所述纯胶的制作:流程为裁切—将备在pet膜上的纯胶打t孔—cnc切型—备pet膜,其中,cnc切型工序将对应刚性板次内层焊盘及挠性板开盖区域进行捞空,形成有捞空区域的纯胶,备pet膜工序为在纯胶捞空后,纯胶无pet膜的一面贴合在备pet膜上,然后揭掉捞空后残缺的pet膜,使纯胶一面有pet膜,另一面无pet膜,在后续贴纯胶工序,将纯胶无pet膜的一面贴合在挠性基板上。
23.参照图1,本发明一非限制实施例,所述纯pi保护膜的制作:流程为裁切—将备在pet膜上的纯pi打t孔—esi镭射控深切型—备pet膜,其中,裁切工序为将纯pi保护膜裁切成片状,且纯pi保护膜片状尺寸小于刚挠结合板的挠性板区尺寸,其纯pi保护膜的尺寸外缘距离纯胶层上的捞空边缘0.15mm,用于贴合在挠性板区的内嵌式焊盘上;esi镭射控深切型工序为将pet膜对应刚性板次内层焊盘除外的区域的纯pi保护膜全镭,对pet膜进行半镭,保证pet膜不镭断,然后将全镭后的纯pi保护膜无pet膜的一面贴合在备pet膜上,再将纯pi保护膜上另一面半镭后的残缺pet膜揭掉,使纯pi保护膜一面有pet膜,另一面无pet膜,贴合时,将出pi保护膜无pet膜的一面贴在内嵌式焊盘上。
24.参照图1,本发明一非限制实施例,所述core板的制作:流程为开料—钻孔—曝光/显影,将挡铜位置显影出来—选镀—线路—打t孔—棕化,制得一面为全铜面,一面为只有挡铜区域含铜其它区域为底板的core板。
25.参照图1,本发明一非限制实施例,所述挡铜设计的挡铜延伸进刚性板0.15mm,所述core板为单面线路设计,所述挡铜设计的一面仅在挡铜区域进行线路设计,所述core板设计挡铜的一面与纯胶和纯pi保护膜贴合。
26.参照图1,本发明一非限制实施例,所述刚挠结合板的外层制作流程为打靶—裁边—棕化—co2镭射—第一次压膜/曝光/显影—沉铜—填孔电镀—线路—aoi—阻焊印刷—后固化—co2镭射控深开盖—等离子除胶—喷砂前处理—第二次压膜/曝光/显影—酸性蚀刻—aoi—cnc切开盖槽—开盖—喷砂前处理—镍钯金—压膜/曝光—cnc成型—退膜—切型—成品水洗—整平烘烤—包装,其中,第一次压膜/曝光/显影工序,除开盖区域需要盖co2干膜外,其它位置全部显影掉,第二次压膜/曝光/显影工序,显影出刚性板次层焊盘区域,然后在酸性蚀刻工序蚀刻掉挡铜区域的铜箔,去除残铜;cnc切开盖槽切是的挠性板区靠近工艺边的两条边,使后续开盖时挠性板区开盖容易,提升开盖效率,开盖后在软板区进行镍钯金表面处理以及压膜/曝光,此处曝光为空曝,压膜将所有区域都覆盖一层膜,防止曝光时cnc刮花金面及阻焊表面,进而有效确保产品外观品质。
27.参照图1,本发明一非限制实施例,所述co2镭射控深开盖在挠性板区的开盖区设计co2镭射路径,co2镭射路径外缘与两侧的刚挠交界线重合,有效确保co2镭射控深时烧掉软板区,同时确保刚性板区不被烧掉,确保产品品质。
28.参照图1,本发明一非限制实施例,所述co2镭射的光斑大小为0.15mm,相邻光斑相交,相交重合区域为光斑大小的3/4,多个光斑相互交叠构成宽度为0.5mm的镭射线,从上往下将流胶和油墨烧掉,其co2镭射效率高,质量好。
29.上述实施例仅为本发明的具体实施例,其描述较为具体和详细,但并不能因此而理解为对本发明专利范围的限制。应当指出的是,对于本领域的普通技术人员来说,在不脱离本发明构思的前提下,还可以做出若干变形和改进,这些显而易见的替换形式均属于本发明的保护范围。